- Main propulsion boilers provide steam to the main propulsion turbines and auxiliary services in order to supply all shipboard steam systems in accordance with demand. (refer to Figure 1). It is designated as a D-type boiler because of the relative positions of the drums and side header which form the letter D. All D-type boilers are designated as uncontrolled superheat boilers because all the steam generated by the boiler must pass through the superheater. Superheater outlet temperature is a result of the combustion gas flow in proportion to the total amount of steam flow through all ranges (0 - 120%). The design characteristics ensure that the temperature will stabilize at set point. The degree of superheat is calculated by subtracting steam drum temperature from the actual reading on the superheater outlet temperature gage. In this lesson we will examine the components of the boiler and then we will bring everything together by describing how water and steam is generated and circulated through the boiler. The flow path of combustion gases through the boiler will also be discussed.
D TYPE BOILER
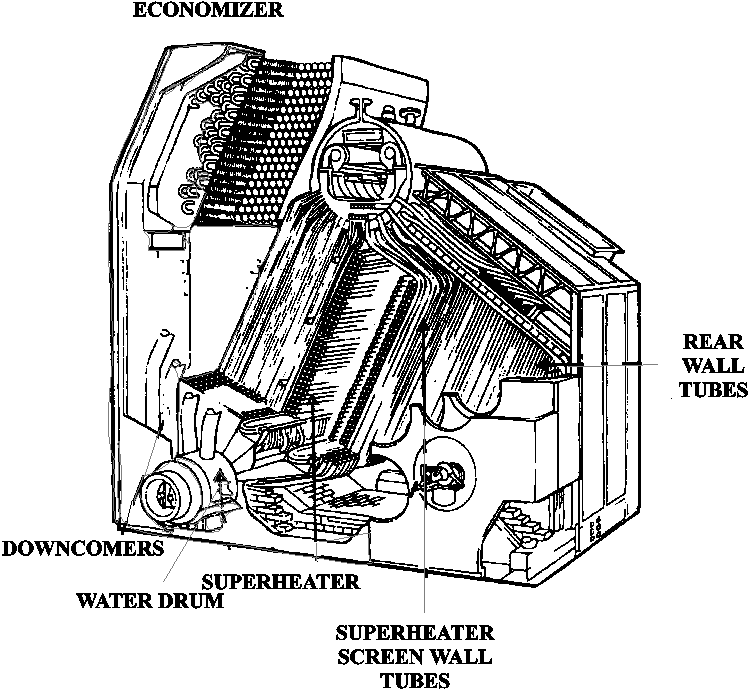
Figure 1
- The economizer is a multi-pass heat exchanger located above the main generating bank at the base of the exhaust stack, so that combustion gas will give up a lot of its remaining heat to the incoming feedwater before passing out the stack (Refer to Figure 2) The incoming feedwater absorbs about 100°-200°F sensible heat from the exhaust gases. Fins are installed on the economizer tubes to increase the heating surface area further, helping to increase efficiency.
ECONOMIZER
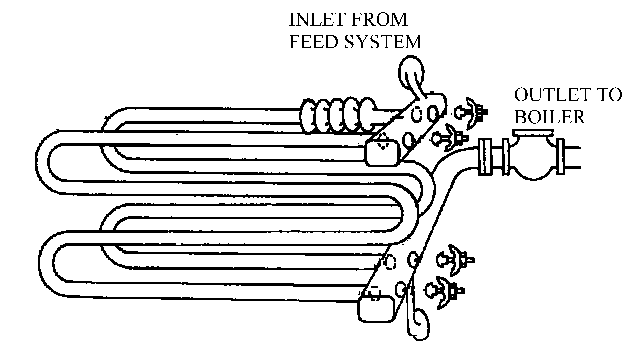
Figure 2
- The steam drum is located at the top of the boiler to provide an upper reservoir for the water covering the generating tube bank. Water is distributed from the steam drum to the lower drums and headers by pipes called downcomers. Generated steam is also collected and is separated from the water in the steam drum. Boilers are also equipped with safety valves to relieve excessive pressure. The valves are located on the steam drum and superheater outlet. They are designed to relieve sufficient pressure to safely steam the boiler at 120% with boiler steam stop valves closed (refer to Figure 3). These valves are discussed in detail in lesson 62B-206.
- Air vents or air cocks are installed on top of the steam drum to expel air from inside the steam drum during cold boiler light-off or when filling the boiler. The air vents or air cocks are shut when the boiler starts generating steam.
SAFETY VALVE CONFIGURATION
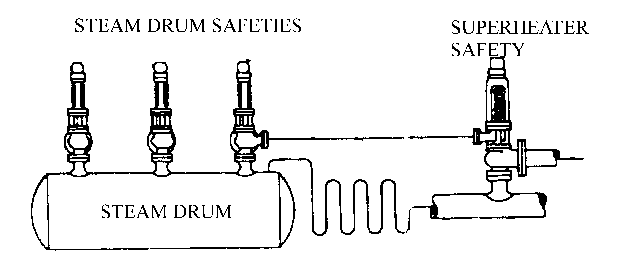
Figure 3
- The internal fittings in the steam drum help distribute the water evenly throughout the drum, separate the generated steam from the water and remove moisture from the steam before it leaves the boiler (refer to Figure 4).
- Lower baffle plates or apron plates Separate the incoming feedwater and generated steam and direct the steam to the separators.
- Primary separators (cyclone separators) Separate most of the water from the steam by giving it a cyclone or rotary motion so that the water particles are expelled from the steam by the centrifugal forces. These separators are vertically mounted in the steam drum so that the steam rises out the top and the water falls back into the steam drum.
- Secondary separators (chevron dryers) Remove additional moisture from the steam by changing the direction of steam flow several times. The steam passes on but the moisture cannot make the direction change with the steam. These separators are mounted above the primary separators and direct steam to the dry box which collects the steam at the top of the steam drum, directing it to the steam outlet piping to the superheater.
- Feedwater leaves the economizer and enters the boiler through the internal feed pipe and becomes "boiler water." Perforations along the side of the feed pipe allow water to be distributed evenly throughout the steam drum (refer to Figure 4)
STEAM DRUM INTERNALS
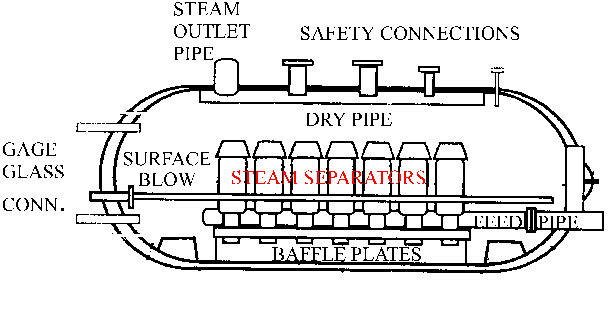
Figure 4
- Since suspended solids may accumulate on the surface of the water in the steam drum, there must be means of removing them. The surface blow pipe is used to remove these light suspended solids from the surface of the water and to reduce the total dissolved solid content of the boiler water. Suspended solids usually consist of oil, salt contaminants, or excessive treatment chemicals which can cause foaming on the water surface. Dissolved solids usually consist of salt contaminants and treatment chemicals that are in solution.
- The D-type boiler uses the principle of accelerated natural circulation to circulate water through the boiler. To enable this principle to work, relatively cool water will naturally circulate through large diameter pipes to distribution points low in the boiler. The downcomers are these large diameter pipes connecting the steam drum with the water drum and lower headers to ensure proper circulation by delivering water from the steam drum to the water drum and lower headers. The downcomers are located between the inner and outer air casing to protect them from the direct radiant heat of the furnace.
- The water drum is located at the bottom of the boiler below the main generating bank and acts as a lower reservoir of water for distribution to the main generating bank. Also, this large drum serves as a collection point for solids (sludge) that precipitate to the bottom that are removed by bottom blowdown.
- The sidewall header is located along the furnace sidewall connecting sidewall tubes from the furnace floor to the steam drum. It distributes water to the sidewall tubes and provides another blowdown point for sludge removal. The sidewall tubes are two inch tubes which protect the boiler sidewall refractory from the direct heat of combustion and generate a small amount of steam.
- The lower rearwall header is located along the furnace rearwall from the furnace floor to the steam drum or upper header to provide a lower junction for rearwall tubes. It distributes water to the rearwall tubes and provides yet another blowdown point for removal of sludge. The rearwall tubes are two inch tubes which protect the boiler rearwall refractory from the heat of combustion and generate some steam.
NOTE: By using wall tubes, more of the heat in the furnace is absorbed by water and less refractory material is required, thereby increasing boiler efficiency and reducing the boiler weight.
- The upper rearwall header is often called the "floating header" because of its free-standing design. It is located along the rearwall of the furnace roof to provide an upper junction for the rearwall tubes. It collects the steam generated in the rearwall tubes and direct it to the steam drum through riser tubes.
- Riser tubes are large tubes located above the furnace roof to provide a connection between the upper rearwall header and the steam drum.
- Superheater screenwall tubes help protect the superheater from direct radiant heat of the furnace. The screen tubes consist of two to three staggered rows of two inch tubes which are usually connected from the steam drum to the water drum. Some boilers have a screenwall header installed parallel to the superheater along the furnace floor as a lower connection and a blowdown point for sludge.
- The steam passes through the superheater picking up sensible heat (about 300-400° F) which increases the energy of the steam, allowing it to perform more work. The superheater is composed of superheater headers which distribute steam to the superheater tubes or elements and direct it from the inlet to outlet piping. These headers and elements can be either vertically or horizontally mounted. (Refer to Figure 5).
SUPERHEATER
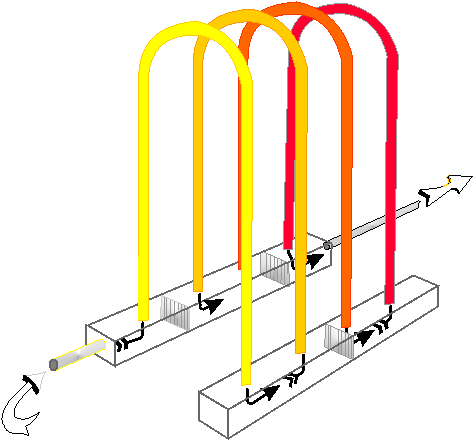
Figure 5
- The bulk of the steam generated by the boiler is formed in the main generating bank because it has the largest heating surface. This is a large group of one inch tubes which run from the water drum to the steam drum and are located behind the superheater.
- Since these boilers are uncontrolled superheat and the plant is designed to use lower temperature steam in many applications to help reduce construction and maintenance costs, the steam needed for these services must pass through a desuperheater. The desuperheater is a multi-pass tube bundle which is located in the water drum in most boilers. There are several boilers which have the desuperheater in the steam drum. As the superheated steam passes through the tube bundle, it gives up heat to the boiler water in the water drum.
- The boiler is protected from the high temperatures of combustion by the refractory. Refractory lines the inside surface of the inner casing enclosing all of the furnace area and extending to the outer row of generating tubes. There are several different types of refractory which work together to protect the boiler.
- Firebrick is a heavy casted refractory used as the outer layer of refractory and is exposed to the direct flames of combustion. It has poor insulating qualities, but it will withstand direct flame contact.
- Insulating brick is a lightweight casted refractory used between the insulating block and firebrick. It has good insulating properties, but it will not withstand direct contact with flame.
- Insulating block is a pressed fiber material used next to the inner casing. It has the highest insulating properties of the various refractory, but it will not withstand direct contact with flame.
- Burner tiles are preformed refractory used to form burner cones around where the burner assembly protrudes into the furnace. Burner tiles are a specially shaped, heavy casted refractory used next to the insulating brick around the burner openings. They have poor insulating qualities, but they will withstand direct flame contact.
- High temperature castable refractory is used to fill in gaps in refractory or where shaping is needed to cover irregular shaped items. It is used to patch refractory or to smooth uneven areas between brickwork. It is packaged dry and must be mixed with water prior to use, very much like cement or plaster.
- Baffle tiles are a specially shaped refractory made of silicon carbide for use in some boilers to form baffles on superheater screen tubes. These baffles direct the flow of combustion gases across the superheater to help maintain the temperature within design parameters.
- When the refractory is installed and stacked, it must be held in place. Anchor bolts are used for preformed refractory. The anchor bolts are connected to the inner casing to support and retain the refractories in position.
- Since the boiler expands and contracts with heating and cooling, expansion joints are built into the refractory to allow for the thermal expansion and contraction.
- Since the boiler expands and contracts as it heats up and cools down, sliding feet are installed to allow the boiler to move easily. The feet are located below the boiler, usually under the front end of the sidewall header and water drum. There is a greased phosphor-bronze friction plate on which these feet will move. The planned maintenance system (PMS) requires lubricating the sliding feet every month. Some newer ships have permalube sliding feet which never require lubrication. Failure of the sliding feet to move can cause cracks in the air casing and can cause header handhole plug leaks. Movement indicators are installed on the sliding feet which have to be checked prior to light off, during warm up, and after the boiler is on line to ensure positive movement of the sliding feet. Each time sliding feet are checked the results should be logged in the fireroom operating log. (Refer to figure 6)
SLIDING FEET CONFIGURATION

Figure 6
- The boiler is enclosed by casings which provide an airtight boundary from the boiler furnace up through to the stack area. The inner casing encloses the boiler fireside area to the base of stack to provide an airtight lining between the combustion air space and furnace to contain the products of combustion within the boiler and support the refractory materials. The outer casing encloses the entire boiler from the bilge to the stack to provide double encasement so the boiler air pressure is not affected by the fireroom atmosphere. The combustion air flows through this space between the inner and outer casing and is directed to the air registers. The stack is located above the boiler economizer and extends to above the superstructure to carry boiler combustion products safely away from the ship. The inner stack or smoke pipe provides a path for combustion gases to the atmosphere, the outer stack supports the inner stack and provides a space to receive incoming combustion air to the boiler and protects personnel from the hot inner stack surfaces.
- The fireroom watch team must be able to monitor the exhaust gases to help maintain a clear smoke free stack. Smoke indicators and periscopes are installed to allow monitoring of the stack gases leaving the boiler. The smoke indicator is an electro-mechanical device and the periscope is an optical device. All ships have periscopes and many have electro-mechanical smoke indicators or stack gas analyzers. These devices are located above the economizer at the base of the stack so that combustion gases leaving the boiler must pass through its line of sight or the sensing element. From monitoring the stack gases, the combustion process can be adjusted for maximum efficiency or a casualty situation can be detected (Refer to Figure 7)
TYPICAL PERISCOPE CONFIGURATION
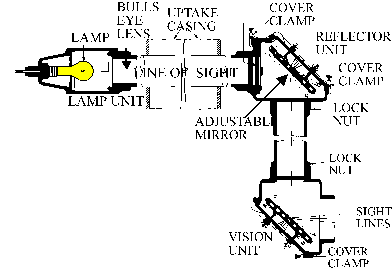
Figure 7
- Maintaining proper boiler water level is one of the most critical aspects of boiler operation. To be able to monitor this critical parameter water level indicators are installed. There are two types, a direct reading gage glass mounted on the steam drum and a remote water level indicator. The gage glass gives a direct measurement of the steam drum water level. The remote water level indicator gives an inferential indication of the steam drum water level.
- The direct reading gage glass may be isolated or removed for maintenance if necessary but, at least two remote water level indicators must be installed and working. (Refer to Figure 8).
REMOTE WATER LEVEL INDICATOR
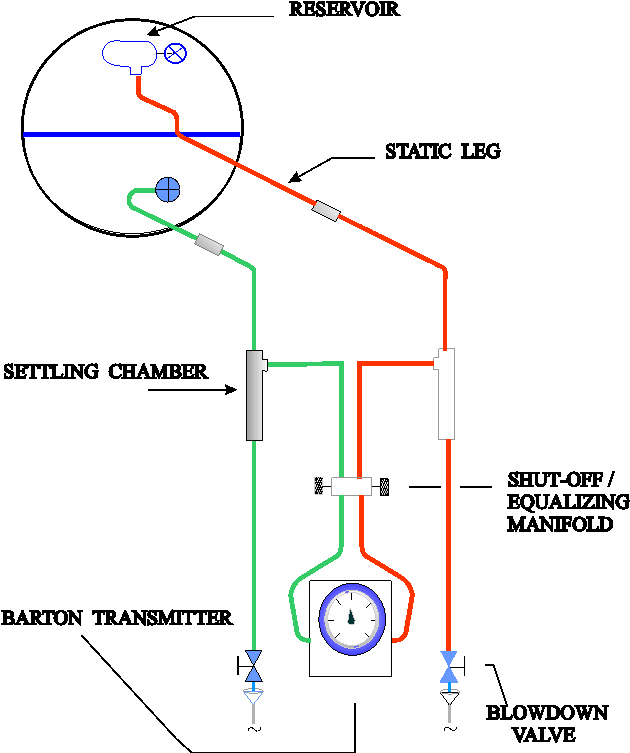
Figure 8
- There are usually two remote water level indicators in the fireroom for each boiler. They are located on the lower level and the BTOW/console station. There is also a remote indicator located at the throttle station for the engine served by that boiler.
- There are high and low water alarms installed in the remote water level indicators. They are set to alarm when the steam drum water level reaches 7 inches above normal or 6 below normal inches on most steam ships.
- Because air casing fires sometimes occur in the boiler, a steam smothering system is installed between the inner and outer casings. This piping comes from the 150 psi desuperheated steam system and is perforated to allow the steam to fill the casing and smother the fire. The piping is located at the lower portion of the casing under the furnace floor and/or brickpan. Steam can be admitted to the furnance by filling the air casing and then opening the air registers. (Refer to figure 9).
STEAM SMOTHERING CONFIGURATION
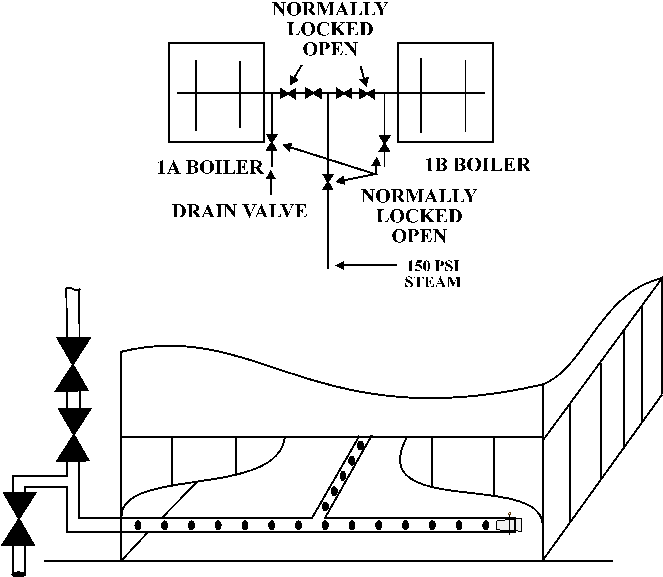
Figure 9
- Once the steam flowing through the superheater is what keeps it from overheating, there must be a means of providing a flow prior to any steam pressure forcing a flow. This means is called the superheater protection steam system. The inlet is connected to the steam drum steam outlet piping and outlet is connected to the desuperheater outlet piping. This arrangement provides steam flow through the superheater during light-off and securing. It is also the entry point for the steam used to provide a steam blanket lay-up. The steam bled off the boiler to provide the flow is routed to the auxiliary exhaust system. When the boiler is being secured, this system needs to be aligned to prevent over-pressurization of the boiler because it is still generating steam. This system is commonly called the superheater bleeder. (Refer to figure 10)
SUPERHEATER PROTECTION SYSTEM
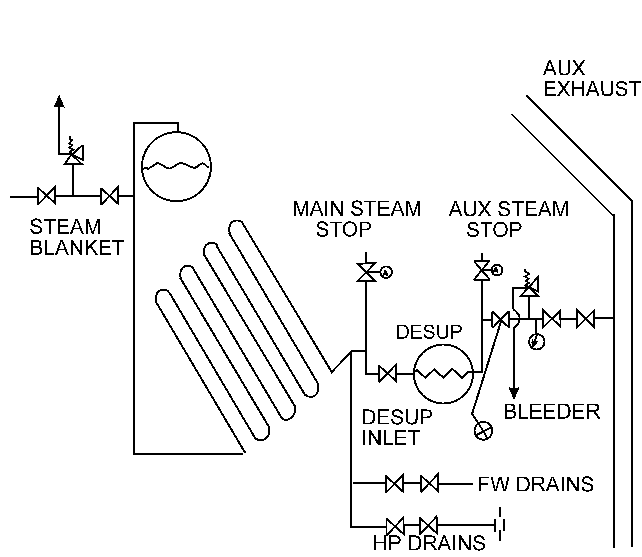
Figure 10
- Fuel oil burners are located on the boiler front and extend into the furnace to provide a means of firing the boiler. Depending on boiler design two to six burners are installed in the boiler. (Refer to Figure 11).
BURNER ASSEMBLY
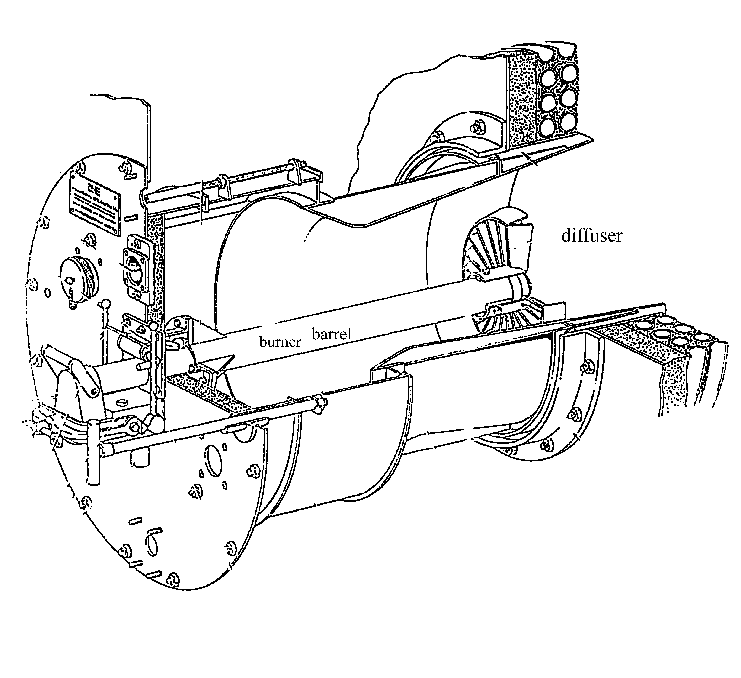
Figure 11
- The burners deliver fuel and air to the boiler furnace in the proper mixture to obtain optimum combustion. The two main components of an oil burner are the atomizer assembly and the air register assembly. The atomizer divides the fuel oil into very fine particles, the air register admits combustion air to the furnace and promotes mixing of the air and the fuel oil spray.
- The types of atomizers used on ships are straight mechanical, steam, and vented plunger, as described below.
- In straight mechanical atomization, all the oil pumped to the atomizer is sprayed into the furnace. The firing rate of this type of burner is controlled by varying the supply fuel oil pressure and changing sprayer plate sizes.
- In steam atomization, steam is used to help atomize the oil into minute particles and to project a cone-shaped spray of atomized oil into the furnace.
- The vented plunger type atomizer is designed to permit a wide range of operation using the straight mechanical pressure atomization principle without the need to change sprayer plate sizes or use steam atomization. It is found in 1200 psi boilers.
- Because the combustion gases leave ash or soot deposits on the tube surfaces which inhibit efficient heat transfer, the soot must be removed. Soot blowers use steam to blow soot off of the tube surfaces. In addition to acting as an insulator, this soot forms sulfuric acid when it becomes wet and eventually corrodes the tube metal.
- Boilers have varying numbers of soot blowers but, there are two basic types, rotary and stationary. They use unreduced desuperheated steam as the motive force which is reduced in the element by an orifice to 300 psi for rotating units and approximately 150 psi for stationary units. Using relatively hot steam at a reduced pressure minimizes moisture in the steam which can lead to erosion or acid corrosion.
- The rotary type of soot blower has multi-nozzle elements. The soot blower head steam valve is actuated by a cam when the element is rotated. The element can be turned by a crank, chain, or an air or electric motor. Steam is admitted from the head into an element which incorporates uniformly spaced nozzles/holes to evenly distribute steam along the area covered. (Refer to figure 12)
ROTARY SOOT BLOWER
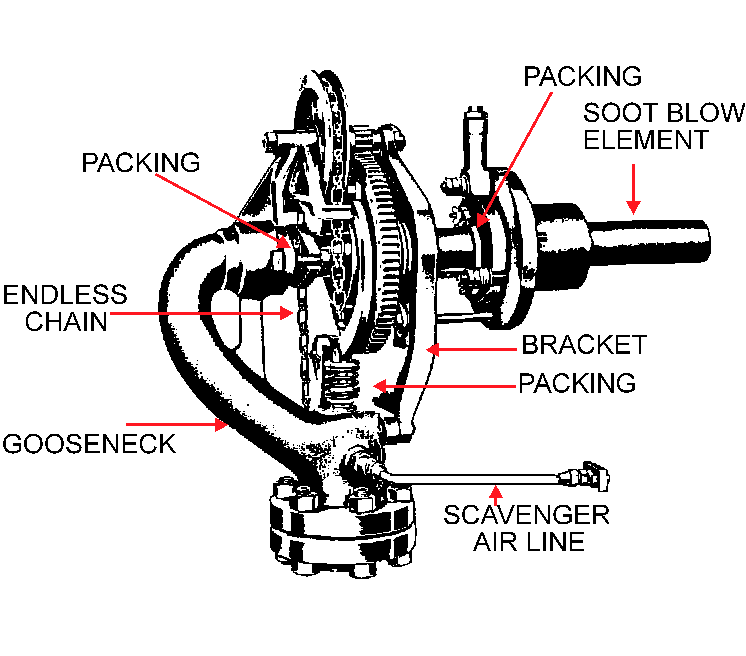
Figure 12
- The stationary type of soot blower usually has one or two rows of nozzles directed to the area immediately near the drums of the boiler. Steam is admitted for a short duration by a manually or power actuated stop valve.
- The soot blower element must be kept cool and clean during operation. To accomplish this, a small amount of air is piped into the element through a small air line. This air is called scavenging air and comes from the combustion air that pressurizes the boiler air casing. This allows a small amount of air to enter the soot blower element to keep it cool and clean. There is a check valve installed in this line to prevent steam from entering the air casing during soot blower operation.
- The operation of soot blowers is called "blowing tubes." Tubes are blown on the following minimum occasions:
- After leaving port
- Before entering port
- After making heavy smoke
- Once each week when steaming
NOTE: EOSS requires tubes to be blown prior to securing a boiler, if possible.
- Since the boiler water chemistry control systems, Chelant or Coordinated Phosphate, both settle sludge to help maintain water purity, there must exist a means to remove this sludge. The bottom blowdown system is used to remove sludge from the water drum and the lower headers. The surface blowdown system is used to remove suspended particles in the water and provide a means of changing out the water in the boiler to lower the conductivity and dissolved substances. Both systems share a common piping arrangement with an overboard guarding valve and overboard discharge valve. (Refer to figure 13)